(Boy slaps himself on the forehead...)
Here's a thought...
Just like folks are making shop made knobs, how about shop built feet / levelers? Here's the thought...
A 3/4" thick disc, maybe 2" dia, center drilled for a 5/16"-18 Tee Nut (not T-nuts like for T slot, but Tee nuts that you drive into wood).

Then a Tee nut in the bottom of the base (so the force is pushing the Tee nut into the wood, not out.)
Take a 5/16-18 star knob like the ones at T-nuts.com
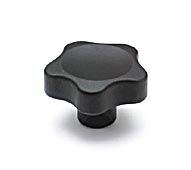
and some plain threaded 5/16"-18 x 3" studs...
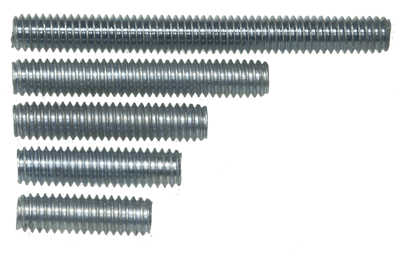
Epoxy the star knob into the stud, run it through the tee nut in the base, run it into the tee nut on the foot and epoxy it in place...
Am I on the right track or have I gone over the edge?
Here's a thought...
Just like folks are making shop made knobs, how about shop built feet / levelers? Here's the thought...
A 3/4" thick disc, maybe 2" dia, center drilled for a 5/16"-18 Tee Nut (not T-nuts like for T slot, but Tee nuts that you drive into wood).

Then a Tee nut in the bottom of the base (so the force is pushing the Tee nut into the wood, not out.)
Take a 5/16-18 star knob like the ones at T-nuts.com
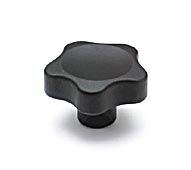
and some plain threaded 5/16"-18 x 3" studs...
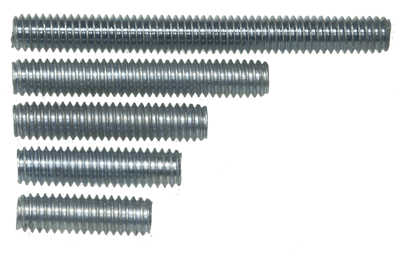
Epoxy the star knob into the stud, run it through the tee nut in the base, run it into the tee nut on the foot and epoxy it in place...
Am I on the right track or have I gone over the edge?
Comment