This weekend I began the buildout of my ultimate tool stand. There were many good ideas included in this thread, some of which will be incorporated.
This all started with acquiring 4 sheets of MDF. I was not impressed with the selection of the plywood at Home Depot or Lowes, at least at the price point i was willing to pay, so I decided to stick with the MDF. I had the stores rip the pieces in half so I could handle them by myself. At nearly 100 pounds, I was not too keen on being a hero. Besides, the widest piece I needed was 24". Might as well let then do it.
I got to try out my new grizzly track saw....

I also acquired one of those foam insulation boards to use as a cutting backer board. That worked quite well.
When all was said and done, on Saturday I had done 90% of the cutting to get to the components on the cut list.
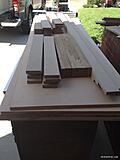
Since Sunday was filled with other projects and my daughter's graduation. Monday was the next "sawdust" day. And I set out to build the torsion box.
My apologies for not having pictures of the internal grid....I simply was "on a roll" and didn't stop to take pictures of the guts of the torsion box.
Some comments about this...
1. The internets can be a wonderful thing. Many people who have built this previously have provided their comments and insights which saved me many hassles from trial and error. This was true for the dado's on the torsion box.
2. Using the setup for my freud 208 stacked dado to get to 3/4" and then adding one of the thin shims was just enough for the pieces to go together easily without breaking a single one.
3. I don't know how you could cut the internal members of this and the sides well without a table saw which enables the more precise repeatablility of of cuts.
4. Gang and clamp the members together to cut the dados. This allows for correct alignment.
5. Pocket Hole screws don't hurt either, as I used them to attach the outside frame to the bottom of the box.
6. A brad nailer is a must as well.
When all was said and done, this is what I got....

I attached the casters, and set it down on the ground.

May put some poly on the bottom of this thing while I can still get it tipped up. Also have to add the leveling blocks to each end, Which I have cut, but not drilled, yet. Then I will work on adding the cabinet section. It is HEAVY.
This all started with acquiring 4 sheets of MDF. I was not impressed with the selection of the plywood at Home Depot or Lowes, at least at the price point i was willing to pay, so I decided to stick with the MDF. I had the stores rip the pieces in half so I could handle them by myself. At nearly 100 pounds, I was not too keen on being a hero. Besides, the widest piece I needed was 24". Might as well let then do it.
I got to try out my new grizzly track saw....
I also acquired one of those foam insulation boards to use as a cutting backer board. That worked quite well.
When all was said and done, on Saturday I had done 90% of the cutting to get to the components on the cut list.
Since Sunday was filled with other projects and my daughter's graduation. Monday was the next "sawdust" day. And I set out to build the torsion box.
My apologies for not having pictures of the internal grid....I simply was "on a roll" and didn't stop to take pictures of the guts of the torsion box.
Some comments about this...
1. The internets can be a wonderful thing. Many people who have built this previously have provided their comments and insights which saved me many hassles from trial and error. This was true for the dado's on the torsion box.
2. Using the setup for my freud 208 stacked dado to get to 3/4" and then adding one of the thin shims was just enough for the pieces to go together easily without breaking a single one.
3. I don't know how you could cut the internal members of this and the sides well without a table saw which enables the more precise repeatablility of of cuts.
4. Gang and clamp the members together to cut the dados. This allows for correct alignment.
5. Pocket Hole screws don't hurt either, as I used them to attach the outside frame to the bottom of the box.
6. A brad nailer is a must as well.
When all was said and done, this is what I got....
I attached the casters, and set it down on the ground.
May put some poly on the bottom of this thing while I can still get it tipped up. Also have to add the leveling blocks to each end, Which I have cut, but not drilled, yet. Then I will work on adding the cabinet section. It is HEAVY.
Comment